UV-C FOR IDEAL GROWTH
OPTIMIZING HORTICULTURAL ENVIRONMENTS WITH LIGHT PROGRESS.
The global market for vertical farming is experiencing significant growth, driven by technological advancements, environmental concerns, and the need for sustainable food production. UV-C technology plays a critical role in maintaining a healthy and pathogen-free environment in horticulture, with a great success in cannabis cultivation. Whether it’s preventing mold spread, disinfecting surfaces, or purifying water, UV-C contributes to sustainable and high-quality crop production.
INDOOR FARMING…GOES VERTICAL!
The booming market for vertical farming is driven by efficiency, sustainability, and the need to meet growing demand for fresh produce worldwide. Vertical farming involves growing crops in vertically stacked layers or vertically inclined surfaces, often in controlled environments such as greenhouses or indoor facilities.
- Resource Efficiency: Vertical farms optimize space, water, and energy usage. They can operate year-round, independent of weather conditions.
- Fresh Produce Demand: Consumers increasingly seek fresh, locally grown produce. Vertical farming meets this demand by providing high-quality, pesticide-free crops
- Technological Innovations: Advances in LED lighting, automation, and hydroponic/aeroponic systems enhance vertical farming efficiency.
- Technological Innovations: Advances in LED lighting, automation, and hydroponic/aeroponic systems enhance vertical farming efficiency.
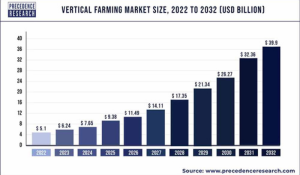
UVC APPLICATION IN HORTICOLTURE; GREENHOUSES AND VERTICAL FARMING.
UV-C disinfection is a powerful technique that finds valuable applications in horticulture, particularly in managing water quality and preventing the spread of plant pathogens in air.
WATER TREATMENT
Proper water treatment is essential for healthy crops. UV-C is an ideal solution for horticulture because it is a clean technology that introduces no chemicals or unwanted by-products into the water.
- Contamination Prevention: UV-C disinfection effectively reduces the risk of contaminants transmission through recirculated drain water. By treating drain water with UV-C, growers can mitigate the risk of contamination and maintain biosecurity measures.
- Cost Savings: Implementing UV-C disinfection for drain water not only prevents virus spread but also leads to cost savings. When disinfected drain water is reused, growers save on water costs and reduce the need for additional fertilizers. Nutrients already present in the drain water can be recycled by plants, promoting efficient fertilizer use. Moreover, UV-C disinfection eliminates reliance on chemical disinfectants, which can be expensive and environmentally harmful.
- Improved Plant Health: By disinfecting drain water, growers ensure healthier plants, better yields, and improved produce quality. This contributes to overall plant vitality and resilience.
- Sustainability: UV-C disinfection aligns with sustainable practices. By reusing treated drain water, growers reduce water consumption, fertilizer usage, and waste. This environmentally friendly approach promotes a more sustainable horticultural system.
Maintaining optimal environmental conditions during cultivation is crucial for plant health and product quality. Factors like temperature, humidity, and air quality significantly impact yield.
Three Approaches: UV-C is employed to control mold and bacterial proliferation in indoor gardens, greenhouses and vertical farming, through three approaches:
- UV-C Surface Disinfection Systems: These systems target HVAC surfaces.
- UV-C Airstream Disinfection Systems: These systems disinfect the entire air flow.
- Stand Alone UV-C: Separate air purifiers system not tied to the HVAC setup
UVC EFFICACY IN CANNABIS GREENHOUSE PRODUCTION
UV-C technology is a powerful tool in the cannabis industry, impacting both cultivation and post-harvest stages. In the ever-evolving landscape of cannabis cultivation, researchers and growers alike are continually seeking innovative methods to enhance both quality and yield. UV-C light, with its germicidal properties, has garnered attention for its potential impact on plant growth and overall product excellence.
Cultivation Phase
- Mitigating Pathogens, Inactivating Spores: UV-C effectively kills microorganisms such as bacteria, viruses, and mold. By integrating UV-C technology, growers can prevent contamination that leads to lost profits and poor quality assurance. UV-C also targets dormant spores, preventing their germination and subsequent spoilage.
- Powdery Mildew and Botrytis Control: While many cultivators focus on mitigating powdery mildew and Botrytis during growth, post-harvest deployments of UV-C are equally crucial. This non-toxic, non-spray disinfection technology ensures clean cannabis products after harvesting, enhancing overall quality and yield.
Post-Harvest Phase
- Quality Enhancement: UV-C light plays a vital role in maintaining post-harvest quality, it ensures that cannabis products meet high standards with a Non-Toxic Solution. Unlike chemical treatments, UV-C is environmentally friendly and poses no risk to consumers.
First and foremost, UV-C treatment led to a remarkable improvement in terpene content, which significantly influences the aroma and flavor profile of cannabis. For connoisseurs and consumers, this translates to a more robust and nuanced sensory experience.
Beyond terpenes, the overall quality of the cannabis was positively affected. The buds exhibited greater visual appeal, with enhanced coloration and trichome development. Moreover, the UV-C-treated plants demonstrated increased resistance to mold and bacteria, a crucial factor in maintaining product safety and longevity. Growers, who often grapple with post-harvest losses due to microbial contamination, may find UV-C light to be a valuable tool in their arsenal.
- Yield Increase: perhaps most enticing for cultivators is the impact on yield. Cannabis plants exposed to UV-C light yielded significantly more biomass. Whether measured in grams per plant or kilograms per harvest, this boost in productivity holds immense promise for commercial operations seeking to optimize their output.
However, practical implementation requires careful consideration of dosage, timing, and strain-specific responses.
While the path forward may involve further research and fine-tuning, the potential benefits are tantalizing.
VERTICAL FARMING AND CANNABIS GROWING
In the cannabis industry, anticipating the future, adapting, and surviving are critical imperatives. This competitive field is arguably more regulated than any other.
From navigating licensing requirements to overseeing construction, numerous barriers confront aspiring cannabis growers. Those who successfully establish a grow operation recognize that space management is a pivotal challenge for optimizing facility efficiency and capacity.
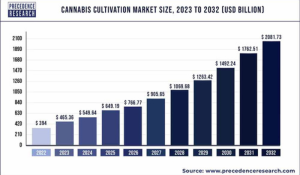
Profitability hinges on simultaneous cultivation and harvesting in a continuous cycle.
Economically and environmentally, cost, space, and time management are paramount, and automation and efficiency play key roles. Vertical farming emerges as one of the most effective strategies.
By maximizing canopy area while minimizing the cost of goods sold (COGs), vertical farming enables the production of high-quality cannabis on a large scale throughout the year. The industry is increasingly recognizing its remarkable efficiency and profitability for cannabis cultivation
The rephrased response emphasizes the importance of anticipating the future, adapting, and surviving in the cannabis industry. It highlights the challenges related to space management and the benefits of vertical farming for efficient and profitable cannabis production.
IN CONCLUSION: A GREENER FUTURE FOR INDOOR FARMING
UV-C, can help eliminate mold in greenhouses, providing an extra layer of peace of mind for controlling contamination, promising solutions for maintaining clean and healthy crops in greenhouse environments, especially for vertical farming. A well-crafted environment—where UV-C plays a vital role—sets the stage for flourishing plants, bountiful harvests, permanently inactivates microbes, including those responsible for spoilage and reduced shelf life.
Especially for cannabis growers, UV-C technology is a valuable asset safeguarding crops from pathogens and ensuring top-notch quality throughout the cultivation and post-harvest processes.
Whether you’re a small-scale home grower or part of a large-scale cultivation facility, exploring UV-C’s role in enhancing cannabis quality and yield could yield fruitful results, Get in touch with our product specialists for a design proposal and a quote
Bibliography:
Ref: Kamel, R.M., El-kholy, M.M., Tolba, N.M. et al. Influence of germicidal ultraviolet radiation UV-C on the quality of Apiaceae spices seeds. Chem. Biol. Technol. Agric. 9, 89 (2022). https://doi.org/10.1186/s40538-022-00358-4
Sadeghianfar P, Nazari M, Backes G. Exposure to Ultraviolet (UV-C) Radiation Increases Germination Rate of Maize (Zea maize L.) and Sugar Beet (Beta vulgaris) Seeds. Plants (Basel). 2019 Feb 24;8(2):49. doi: 10.3390/plants8020049. PMID: 30813484; PMCID: PMC6409551.
A Guide to Drying and Curing Cannabis | Article | Analytical Cannabis